PRECISION CASTING
Comprehensive Range Of Services Providing Endless Capabilities
What is Precision Casting ?
Precision casting is also called investment casting in most cases.
The more commonmethod is: first make the mold cavity of the required blank, then cast wax to obtainthe original wax pattern, and then brush multiple layers of high-temperature-resistant liquid on the wax pattern.
Sand material, wait until sufficient thickness isobtained and then dry it, then heat and bake the wax mold inside to obtain a strongcavity consistent with the required blank, cast the molten metal liguid into the cavity.
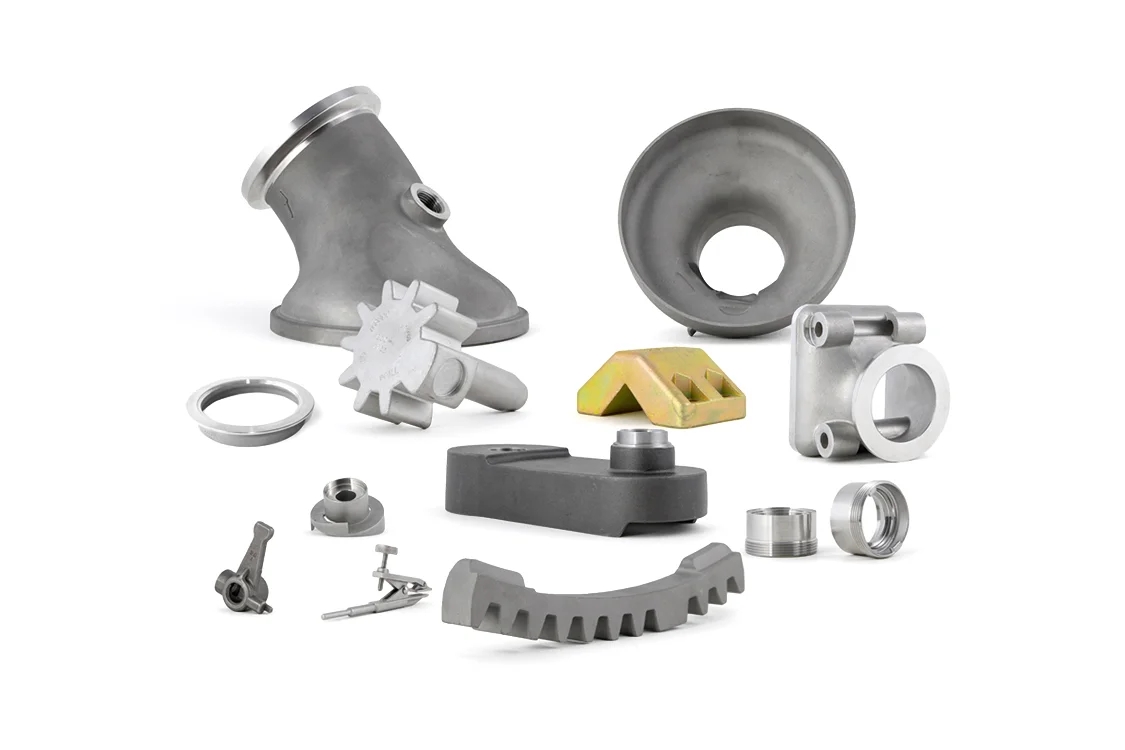
Precision Pasting Process
The precision casting process will vary depending on different materials or products in specific operations, but usually the main steps are: wax pressing, shell making, pouring, post-processing, and inspection
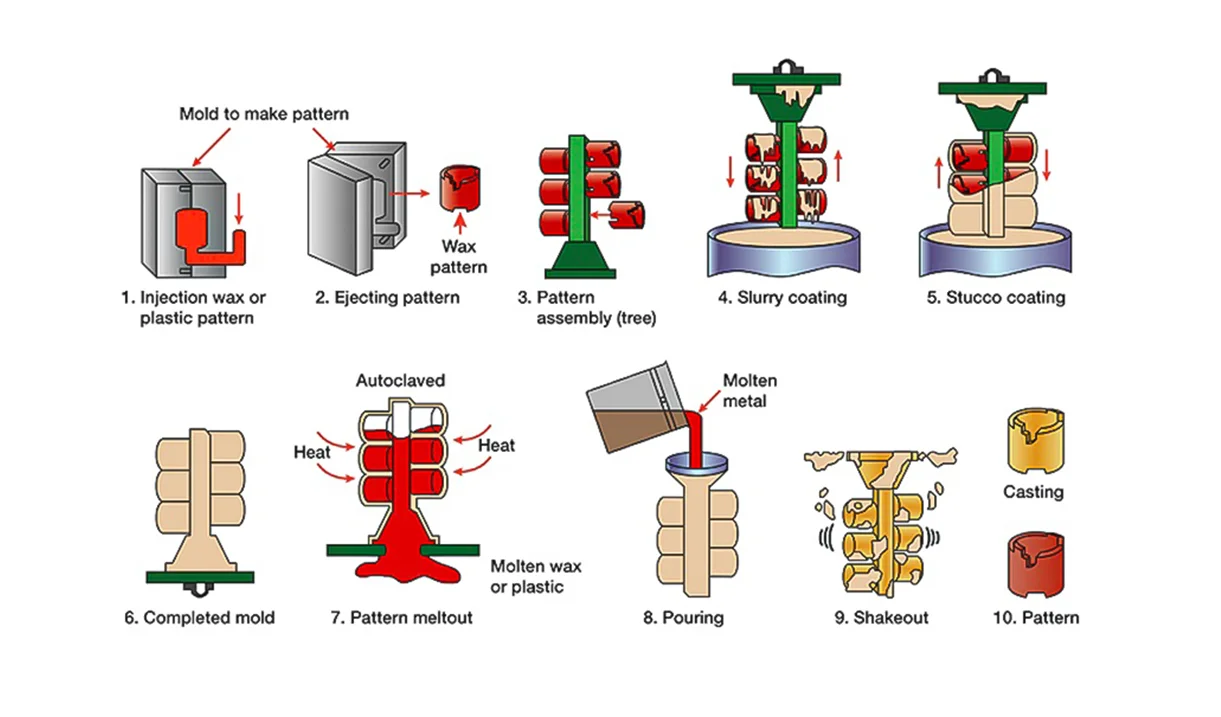
1. Make a model
Design the mold according to the product drawings, and use any method such as machining or 3D printing to make a wax model with good appearance and accuracy, and assemble multiple wax models into an investment casting model. This pattern Known as “trees”, they are shaped like trees. Each wax mold is like a branch, and the trunk serves as a liquid metal pouring channel connecting all the wax molds.
2.Make the shell
Spray the assembled casting model with liquid sand (or other refractory materials), wait for it to dry naturally, then apply the next layer, repeat this many times. The number of sandblasting times and the thickness of the sand particles will vary depending on the parameters and accuracy requirements of the product. It usually takes 3 or 4 days to complete this step. After heating is used to melt all the wax and flow out, the shell is baked at a high temperature close to 1000°C to burn off the remaining wax and evaporate the water, and finally obtain a solid casting model cavity. Every step must be done carefully to create a perfect casting model.
3.Pouring
Operators inject molten liquid metal into the mold cavity in a controlled manner. It is very important to control the pouring process. It is necessary to preheat the mold, avoid the thermal impact of high-temperature liquid metal on the mold as much as possible, and control the pouring speed to avoid casting defects caused by turbulence. Sometimes a vacuum environment must be created to prevent chemical reactions between the molten metal and the air. . After pouring, the metal solidifies in the mold and cools naturally.
4.Post-processing
Operators remove portions of the mold shell with a hammer or impact, and the parts are often finished multiple times after they are removed from the mold by sanding away rough surfaces, jagged edges and other imperfections. Additionally, machining operations such as milling and drilling can be used, as well as a range of surface finish treatments to achieve the desired part surface quality.
5.Inspection
Parts are inspected for quality in the final step. The inspection team uses testing tools to check parts for defects, as well as other quality factors such as dimensions, tolerances, surface hardness, strength, etc.
What are the advantages of precision casting?
Investment casting can obtain accurate shapes and high-precision finished products. It is a casting process with little or no cutting. It is an excellent process technology in the foundry industry and has a wide range of applications. It is not only suitable for casting of various types and alloys, but also produces castings with higher dimensional accuracy and surface quality than other casting methods. Even complex, high-temperature-resistant, and difficult-to-process castings that are difficult to obtain by other casting methods can be produced. Investment casting can be used.
Investment casting is widely used in manufacturing industries such as aviation, automobiles, machine tools, ships, internal combustion engines, steam turbines, telecommunications equipment, weapons, medical equipment, and cutting tools.
Another advantage of the investment casting method is that it can cast complex castings of various alloys, especially high-temperature alloy materials. For example, jet engine blades have streamlined outer contours and cooling inner cavities that are almost impossible to form using machining processes. However, the investment casting process can not only achieve mass production, but also ensure the consistency of castings.
Factors affecting the accuracy of precision casting
The structure of the casting affects the accuracy. The greater the wall thickness of the casting, the shrinkage rate increases; the thinner the wall thickness of the casting, the smaller the shrinkage rate.
The material of the casting affects the accuracy. The higher the carbon content of the casting material, the smaller the linear shrinkage rate; the lower the carbon content, the greater the linear shrinkage rate
The influence of the shell material. If zircon sand, zircon powder, Shangdian sand, Shangdian powder is used, the impact on accuracy will be very low due to its small expansion coefficient.
The impact of mold shell baking is small because the expansion coefficient of the mold shell is small. Even when the mold shell temperature is 1150°C, it is only 0.053%, so it can be ignored.
The influence of investment mold on the linear shrinkage of castings. The wax injection temperature, pressure, and holding time have an impact on the dimensional accuracy of the investment mold. Among them, the wax injection temperature has the most significant impact. The higher the temperature, the greater the shrinkage, followed by the wax injection pressure. The holding time plays an important role in ensuring that the investment mold is formed. The final size of the investment has little effect; when the investment is stored, it will shrink further, but after 12 hours of storage, the size of the investment is stable.
The influence of casting temperature has a significant impact on the accuracy of the finished product. The higher the casting temperature, the greater the shrinkage rate. The lower the casting temperature, the smaller the shrinkage rate. Therefore, it is necessary to adopt the most appropriate casting temperature.
Precision Casting processing application industries
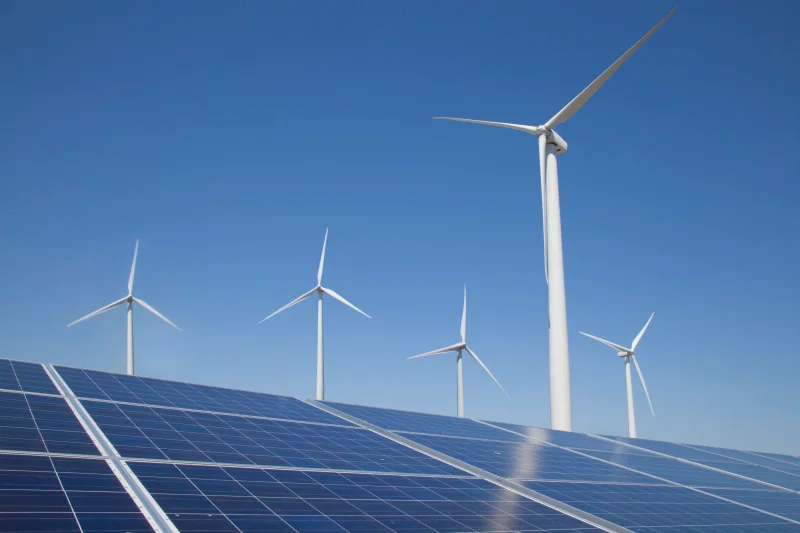
Energy Industry
The energy sector has a very specific use for this manufacturing technology. Wind turbine blades are large, weigh several tons, and require exceptional strength and surface finish. Precision casting processing has unparalleled advantages under the combination of this quality requirement.
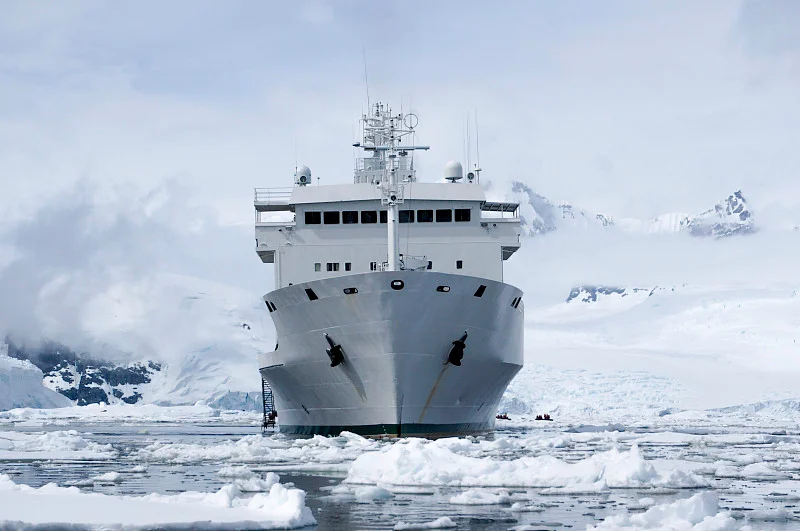
Marine Industry
Investment casting of metal parts is common in the marine industry. The metal panels of ships and submarines are strong and corrosion-resistant, and they are made of special alloys. Investment casting machining is ideal because it is compatible with a wide range of metal alloys.
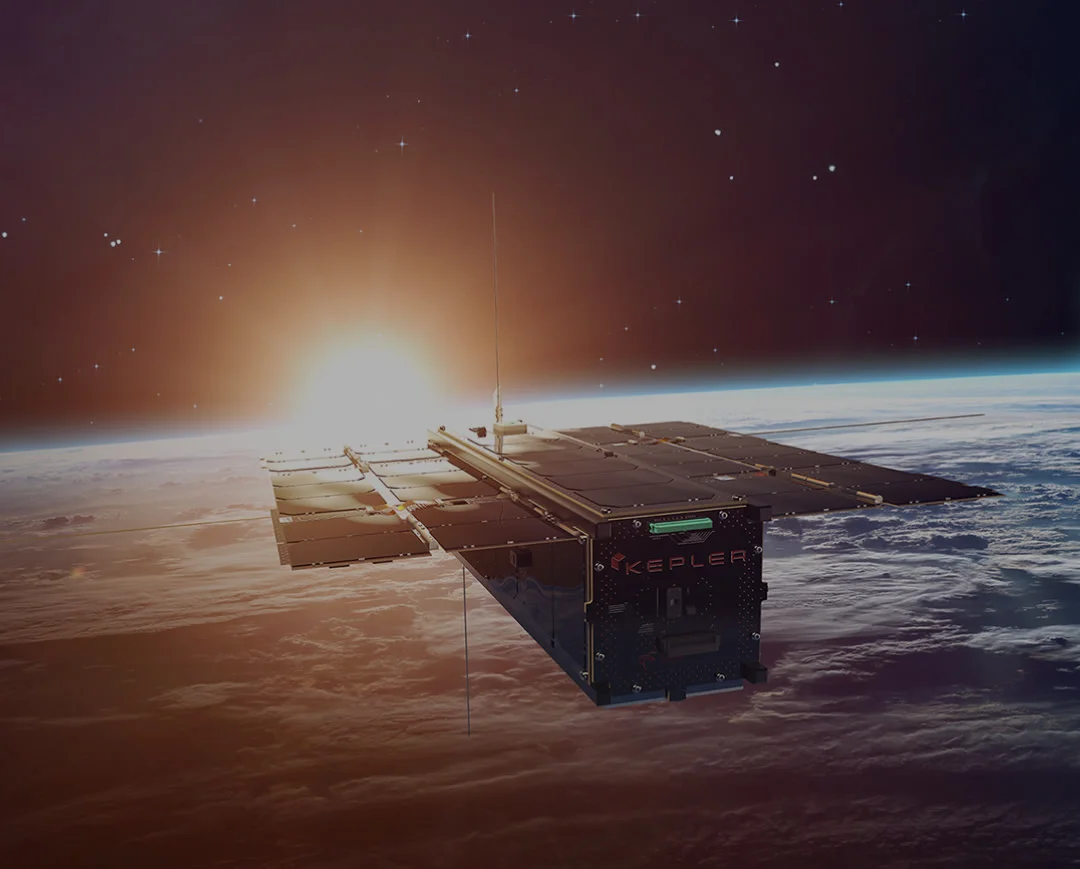
Aerospace technology applications
Precision casting technology can manufacture key components in aircraft engines and fuselages with complex geometric shapes and strength requirements.
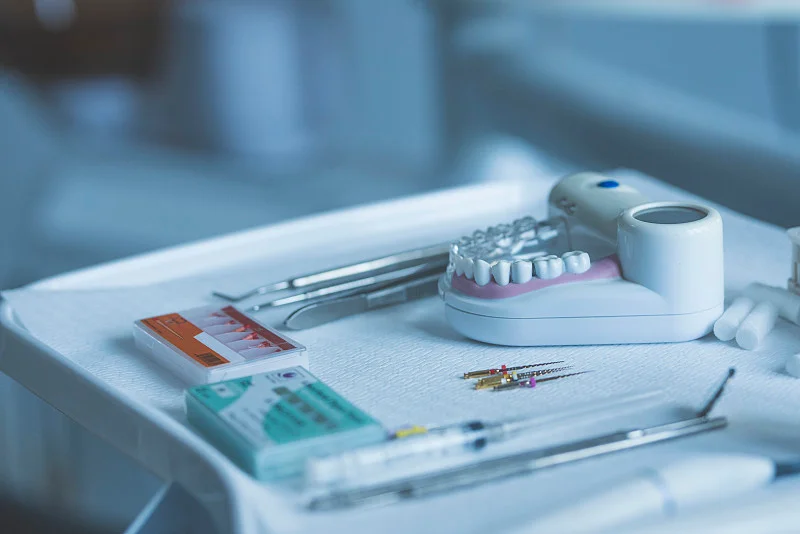
Medical industry
Precision casting processing has advantages in the medical industry. Dentistry, prosthetics, implants and surgical equipment are common applications where the investment casting process has the ability to produce small size parts with excellent surface finish.
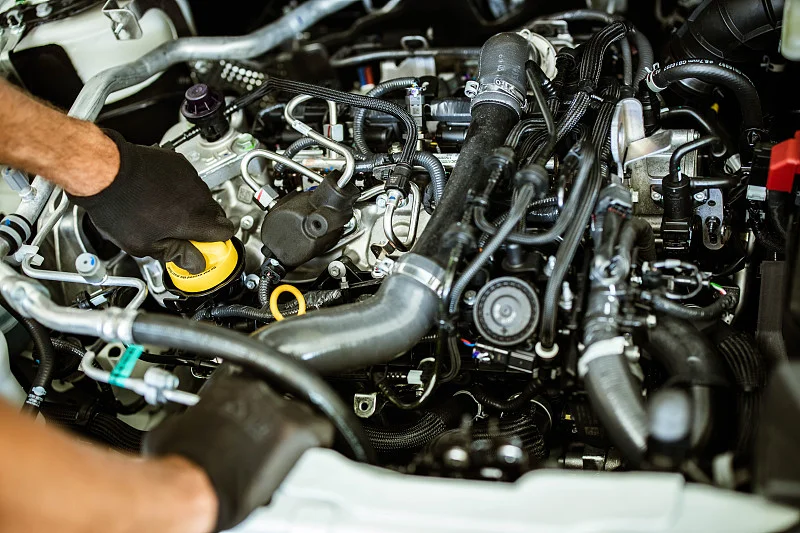
Automotive Industry
Investment casting is ideal for manufacturing high-performance components for the automotive industry, such as drivetrain components, rocker arms, and powertrain components.