POWDER METALLURGY PROCESS
Comprehensive Range Of Services Providing Endless Capabilities
What is powder metallurgy processing ?
Powder metallurgy is a processing method that uses metal powder as raw material and presses and sinters it to make products. The powder metallurgy process mainly consists of three steps in sequence: granulation, molding, and sintering. First, the main material is decomposed into a powder composed of many fine particles; then the powder is loaded into the mold and pressure is applied to form a compact that conforms to the appearance and size of the part; finally, the compact is sintered.

Advantages of powder metallurgy processing
There are no restrictions on the appearance and structure of parts. You can use simple steps to obtain products with irregular appearances, or products with holes, keyways, and patterns. Complex parts that require irregular curves, eccentricities, radial protrusions or grooves that are not easy to machine can usually only be produced by powder metallurgy products.
The production efficiency is high. The product is molded in one mold and requires almost no additional mechanical processing. Compared with other mechanical processing methods, the total energy consumption of the sintering process is usually less and is generally more environmentally friendly.
Complex parts requiring irregular curves, eccentricities, radial protrusions or grooves can usually only be produced through powder metallurgy products. Parts that require irregular holes, keyways, flat edges, or square holes and are difficult to machine can usually be manufactured using powder metallurgy methods.
There is a lot of freedom in the shape and design of parts, and the materials are also very flexible, so they are very versatile. In summary, the powder metallurgy part process provides tight dimensional tolerances, smaller machining volumes, good surface finishes, and excellent part-to-part reproducibility for medium to high-volume part production.
Save materials, there is almost no waste of raw materials, and unused metal powder can be recycled for secondary use.
The powder metallurgy product process can produce hundreds to thousands of parts per hour, maintaining tight dimensional tolerances between parts
Self-lubricating. Powder metallurgy products can achieve controllable porosity and form finer microstructures. By filling the pores of the material with oil, a self-lubricating bearing is obtained: the oil provides continuous lubrication between the bearing and the shaft, and the system does not require any additional external lubricant.
Applications of powder metallurgy
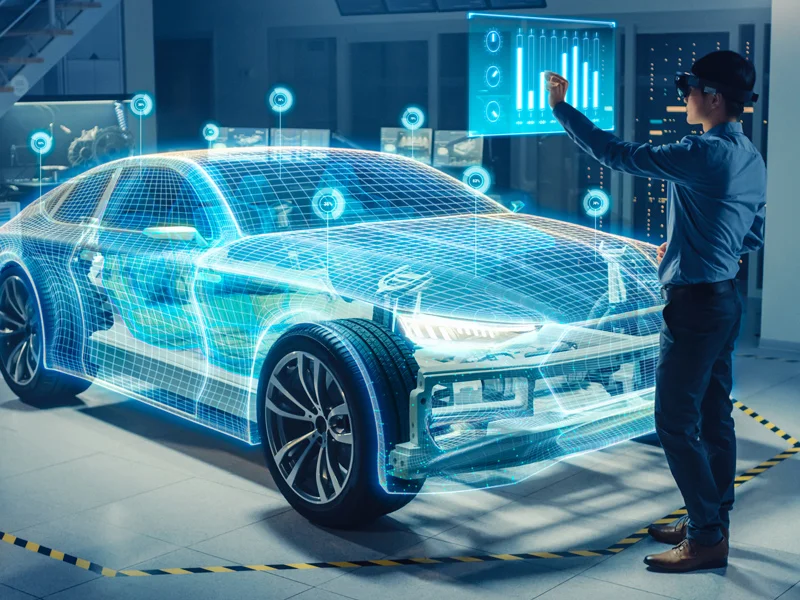
Automobile industry
The automotive industry is a large consumer of PM. Automotive engine parts and other parts that require mass production, automotive metal powder is designed to achieve the best balance of performance and cost, whether it is differential gear sets, steering columns, crankshaft sprockets, exhaust system components, rearview mirror brackets, etc. Valve seats and valve guides as well as accessories, etc., powder metallurgy processing is an integral part of the automotive industry. The value of powder metallurgy to the automotive market is needless to say.
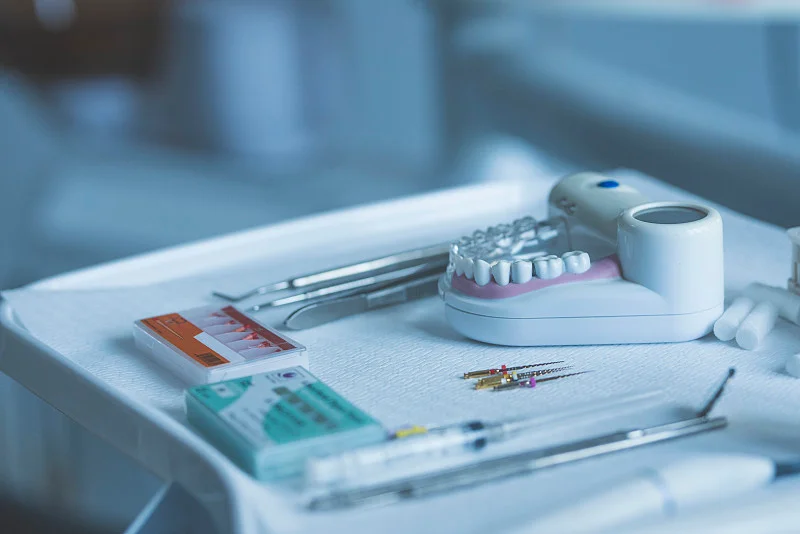
Medical industry
When it comes to machining complex medical device components as well as precision parts for dental equipment, choosing metal injection molding (PM) can reduce costs, reduce material waste, and provide the ability to produce parts that are not feasible using other manufacturing methods.
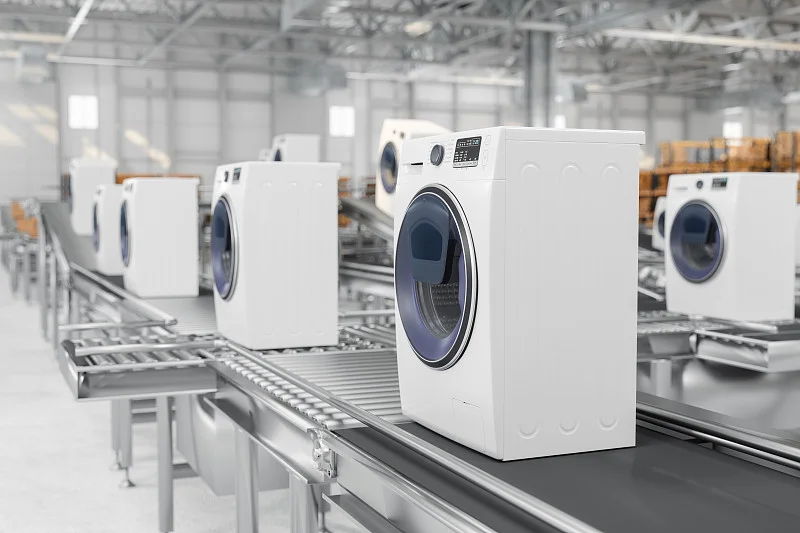
Household appliances
The components and assemblies of home appliances will be completed using powder metallurgy processing (PM), which can manufacture simple or complex structural parts, typically such as internal components of air conditioners, washing machines, microwave ovens, etc.
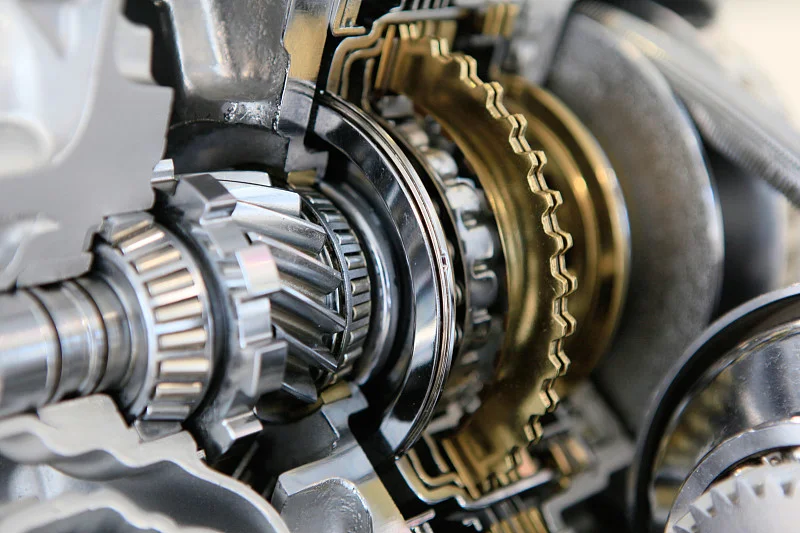
Gears, sprockets
Powder metallurgy gears are widely used in various motorcycles and automobile engines. Through one-time forming and finishing processes, dimensional accuracy requirements can be met without the need for other post-processing processes. Moreover, processing gears from powder metallurgy blanks can increase the strength by about 80%. The overall performance is improved by about 30%, so powder metallurgy is widely used in gear parts.
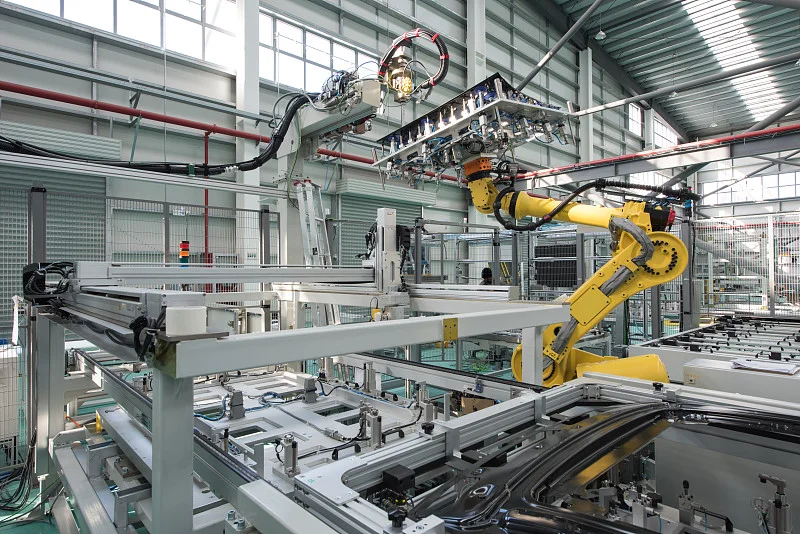
Industrial machinery
Powder metallurgy (PM) has a place in many large-scale construction machinery, agricultural machinery, parts and components of heavy-duty construction and maintenance machinery.
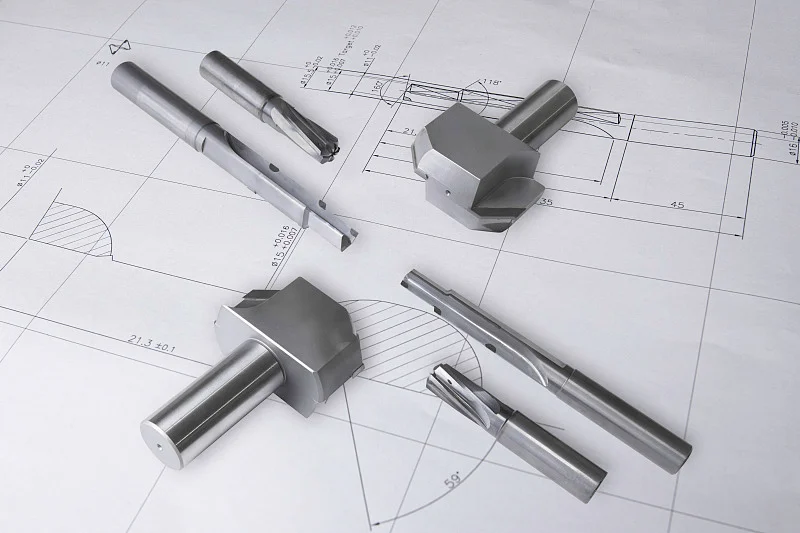
Other industries
include but are not limited to industrial motors, controls, hydraulics, aerospace and hand tools.
There are many types of applications for powder metallurgy processing, including: tungsten and other refractory metals and alloy products; tungsten carbide (WC), titanium carbide (TiC), tantalum carbide (TaC) and other products using Co and Ni as binders Carbide is used to make drill bits, turning tools, milling cutters and wear-resistant tools in cutting tools, and can also make molds; porous materials, such as copper alloys, stainless steel and nickel, are used to make oil-containing sintered bearings, metal sintered filters and textile rings, etc. With the development of powder metallurgy production technology, powder metallurgy and its products will be more widely used.