DIE CASTING
Comprehensive Range Of Services Providing Endless Capabilities
What is Die Casting ?
Pressure casting is characterized by using a mold cavity to apply high pressure to the diethized metal. The four steps of the die casting process: mold preparation, filling, ejection and shakeout. During the preparation process, lubricant needs to be sprayed into the mold cavity. The lubricant can control the temperature of the mold and help separate the casting from the mold. This is the basis of any die casting process. Molds are usually machined from stronger alloys, and the equipment and molds used in die casting are expensive, so the die casting process is generally only used to manufacture large quantities of products. Die casting is particularly suitable for manufacturing a large number of small and medium-sized castings, so die casting is the most widely used among various casting processes. Compared with other casting technologies, die casting has a flatter surface and higher dimensional consistency.
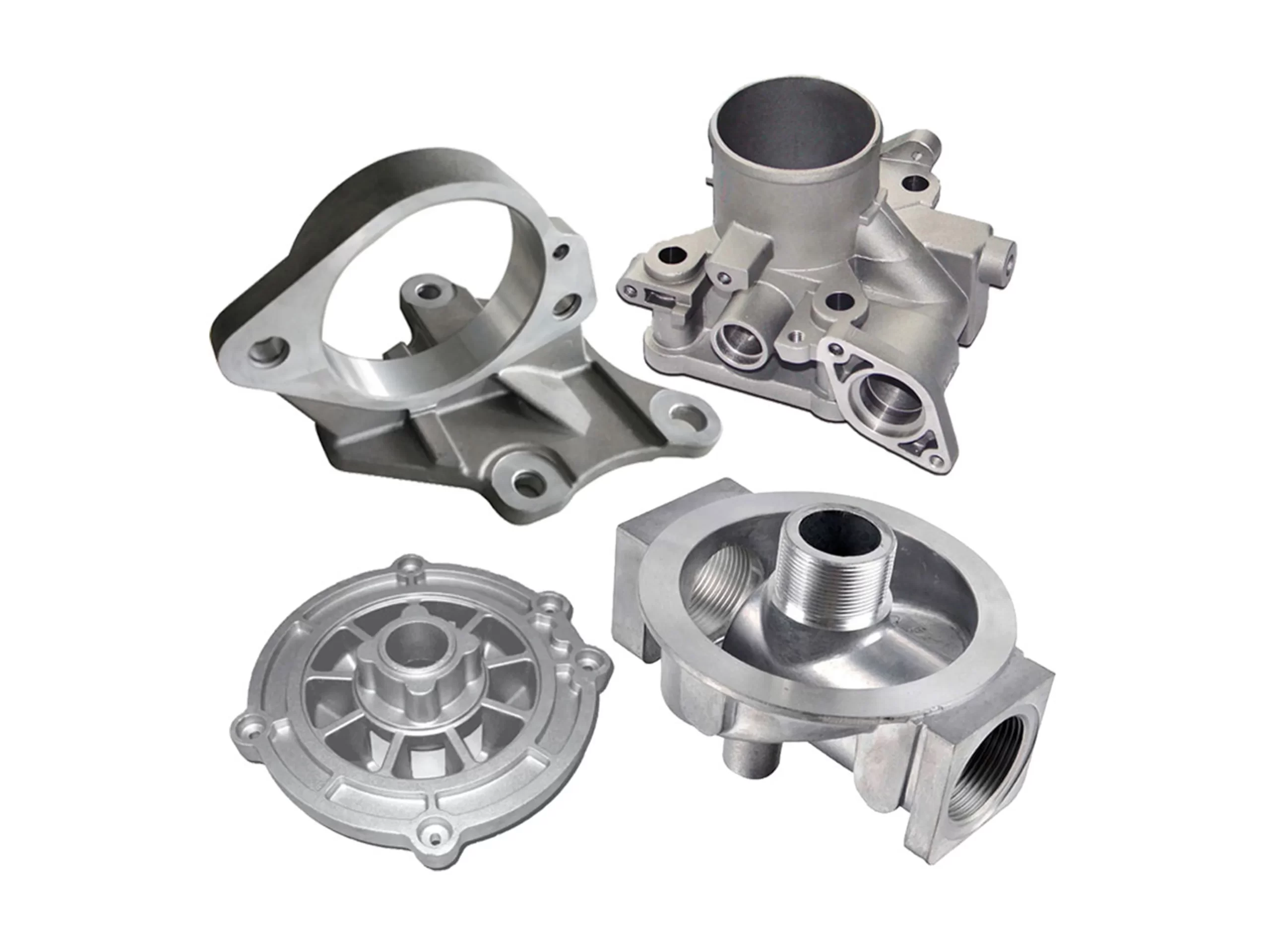
During the preparation process, lubricant needs to be sprayed into the mold cavity. In addition to helping to control the temperature of the mold, lubricant can also help in the demoulding of the casting. After the mold is closed, molten metal is injected into the mold with high pressure to completely fill it, and the pressure is maintained until the casting solidifies. The push rod then pushes out all the castings and can be designed to produce multiple castings in each casting process. The doffing process requires separation of residues. This process is usually completed through a special casting. Other doffing methods include sawing and grinding, and castings can also be directly beaten to improve efficiency.
Types of die Casting processes
According to the different types of die casting, it can be divided into hot chamber die casting machine and cold chamber die casting machine.
The mold closing mechanism of hot chamber die casting machine and cold chamber die casting machine is the same, both adopt hydraulically driven connecting rod mechanical mold closing mechanism. But there are some differences in the injection part. The pressure chamber and the crucible of the hot chamber die casting machine are connected together; the pressure chamber and the crucible of the cold chamber die casting machine are separated. It relies on manual or automatic manipulators to transfer the molten metal from the crucible. The crucible is transferred to the mold.
Hot chamber die casting is difficult to use for die casting large castings. Usually this process is used to die cast small castings; metals with higher melting points cannot be die cast. Generally speaking, hot chamber die casting machines are used for alloys of zinc, tin and lead.
When the hot chamber die casting process is not applicable, cold chamber die casting can be used, including aluminum, magnesium, copper and zinc alloys with higher aluminum content. The metal needs to be melted off first in a separate crucible. The molten metal is then transferred to an unheated injection chamber. These metals are injected into the mold through hydraulic or mechanical pressure. The biggest disadvantage of cold chamber die casting is the long cycle time