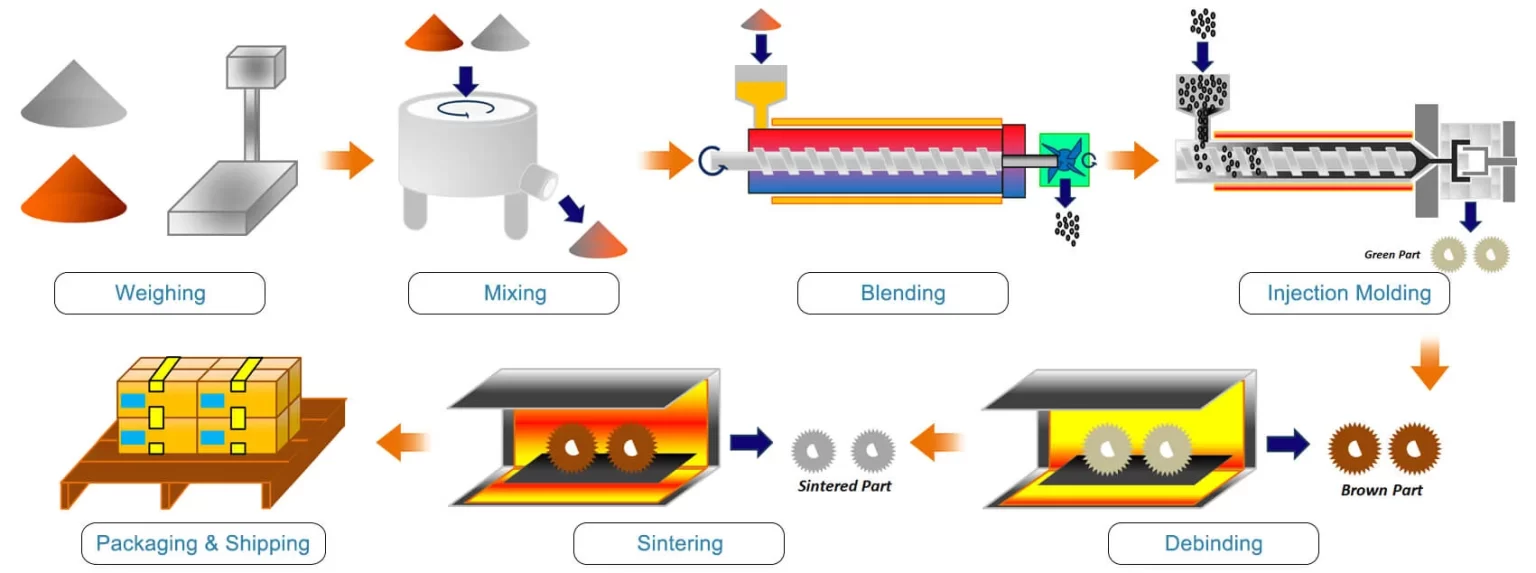
Discover Metal Injection Molding Technology
1.Core Advantages of Metal Injection Molding (Revolutionary Manufacturing Efficiency) Material Utilization>98% Rejected green parts can be recycled without quality compromise 40%-60%cost reduction vs.machining when equivalent density < 2g/cm³ Complex structure